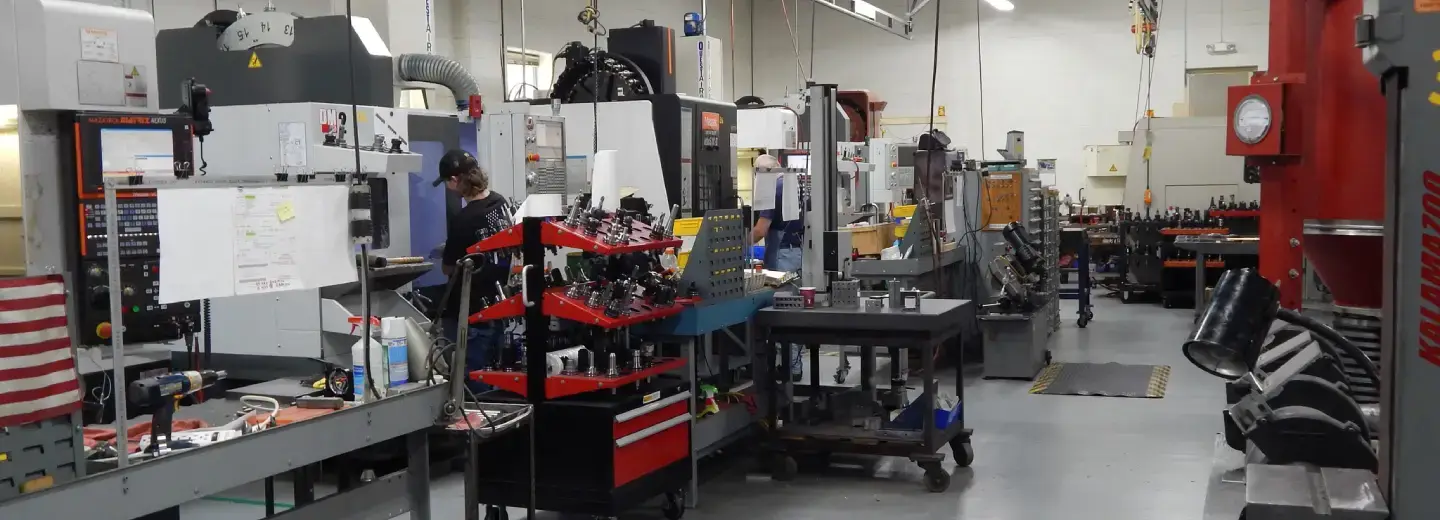
Products >> Turnkey
Iodized Salt Refinery process plant is mainly divided into Four Section.
Raw salt is fed into the feeding hopper of suitable capacity which will be made of RCC and it is then transferred to a belt conveyor. This belt conveyor will be fitted with a magnet to remove rubbish metal and will also be provided with a belt weigher with totalizer. The permanent magnet used are Anisotropic Strontium Ferrite Magnets which have highest resistance to demagnetization. It is driven by a three phase motor with built in reduction gear box and food grade belt for transfer of salt from in feed hopper to wet mill. Wet mill is used to grind the salt with the help of saturated brine solution. The ground salt particles size up to 1400 micron. The degree of grinding can be controlled by the gap setting and by the serration of the segments.
This mixture is then passed to the Elutriation tank where in dirt is removed from the slurry. This slurry is then pumped to the washing tank by a slurry pump, wherein impurities are removed from the slurry. The overflow from the washed tank is collected in brine tanks where in manganese dosing is done. This is then pumped to the thickener by a slurry pump for thickening of the slurry.
The thick slurry is then passed through a Pusher Centrifuge which separates salt crystals from the slurry and the liquid is collected in a filtrate tank. This liquid portion is then pumped to the thickener for further processing. Wet dosing is done on separated salt crystals from centrifuge and feeding product inside the Fluid-Bed dryer by Screw Feeder, which is made of SS 316. The crystal forms the layer on the perforated sheet present in the drying chamber of the fluid bed dryer and is dried by means of hot air from above 150°C air heating system. The Finex are removed from the exhaust stream in the cyclone separator and is collected separately. Dry salt from the outlet of the fluid-bed dryer is passed to a bucket elevator.
Bucket elevator feeds dry salt into the hopper. The dry salt is passed out to Vibro Sifter to screen out the oversized particles through suitable mesh size from the dried salt. Oversized particles passed out to Pin Mill/ Roller Crusher to grind the particles to make it required size of 0.85 mm & less. It has a rotor assembly carrying hammers supported on heavy self-aligned bearing system. The discharge will be done through perforated screen at the bottom and salt is passed to the feed in hopper of the blender where in free flowing agent is added. This free flowing salt is then sent to the Finished Goods storage silo.
Free flowing iodized salt is packed in 200 gm/500 gm/1 kg/2 kg. Packing is done by automatic form fill seal machines or manual filling. Packs are packed into a 50 kg bags & stacked in warehouse by Belt conveying system. Belt conveying system is also used for loading the bags into a truck.
Note: Salt loss should not exceed 15%
Applications | |
---|---|
Content Compositions | Raw Salt Percentage |
Sodium Chloride (NaCl) | 94.00 Maximum |
Calcium (Ca) | 0.24-0.40 |
Magnesium (Mg) | 0.10-0.40 |
Sulfate (SO₄) | 1.00-1.50 |
Insoluble | 0.30-1.50 |
Iodine | ------------- |
Anticaking agent | ------------- |
Free flow agent | ------------- |
Moisture | 4.0 |
Particles Size | 4mm-8mm - 60% |
Below 4mm - 30% | |
Below 8mm - 20% | |
Maximum 12mm |